JEPL has pioneered into the manufacturing of Metal Crash Barrier / Highway Guard rail (W-Beam) in Nepal. We have state of the art manufacturing facility supported by well-equipped testing facilities for “W- Beam”. We provide both regular & customized ‘W Beam’ type Crash Barriers with hot-dip galvanizing (HDG) arrangement and stringent quality controls. Our present annual manufacturing capacity of Crash Barrier is 18,000MT.
JEPL manufactures Crash Barrier assembly (W-Beam, U-Post and spacer) as per Govt. of Nepal, Ministry of Physical Infrastructure & Transport Department of Roads (Nepal Road Standard - NRS 2070) and Indian Standard as per MORT&H (Ministry of Road, Transport & Highways).
Our materials are produced from best quality HR Coils from Tata Steel / SAIL / JSW, conforming to IS 5986 / IS I0748 / IS 2062 or equivalent International Standards.
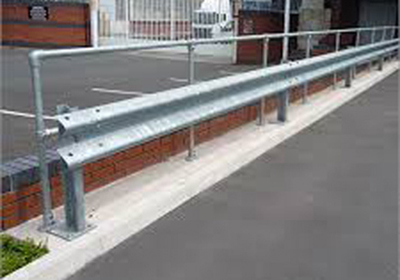
JEPL Facilities for manufacturing Crash Barrier :
JEPL has the state-of-the- art facility for making all types of W-Beam, Post, Spacer, End Terminal, End shoes, Fish Tail. We have 8M / 12M Zinc Galvanizing bath for Galvanizing W-Beam and accessories coupled with Dedicated Mechanical and Chemical Laboratory including Spectrometer for in-house testing.
Metal Crash Barrier is an infrastructural support for road safety which ensures safety and security of people and vehicles during unforeseen circumstances namely, road accidents or mishaps. Crash Barrier absorbs the impact of energy emitted from the colliding vehicle which thus results into minimization of risk and damage to vehicles and passengers.
Metal beam crash barriers are located on approaches to bridge structures, at horizontal curves, and at locations where the embankment height is more than 3m.
Metal Crash Barrier Assembly : All HDG product conforming to NRS-2070 or MORT&H of Indian standard.
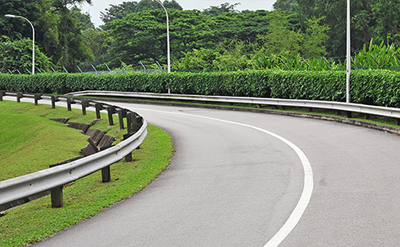
Material specifications :
a. The metal beam rail and the railing post shall be made of corrugated sheet steel beams of the class, section, type, and thickness as specified in the plans.
b. All complete steel rail elements, posts, terminal sections, nuts, bolts, hardware, and other steel fittings shall be galvanized.
c. All railing elements shall be free from rough or sharp edges and abrasions and shall not be kinked, twisted, or bent.
d. Unless otherwise specified, the steel beam elements and terminal sections shall be galvanized (zinc-coated, 550 GSM, minimum single spot).
e. All galvanizing works shall be done after fabrication.
Description | Thickness (mm) | Length (mm) | Quantity (no.) | |
1 | W- Beam (Width – 312mm) | 3.00 | 4320 | 1 |
2 | U- Post 150 x 75 mm | 5.00 | 1800 | 2 |
3 | Spacer 150 x 75mm | 5.00 | 330 | 2 |
4 | Nuts and bolts (button Head & Hexagonal) | 35 | 14 |
Note :
HR Sheet Grade : As per IS 5986 or IS I0748 or equivalent
Fasteners : As per IS 1364 and IS 1367 of grade 4.6 MS
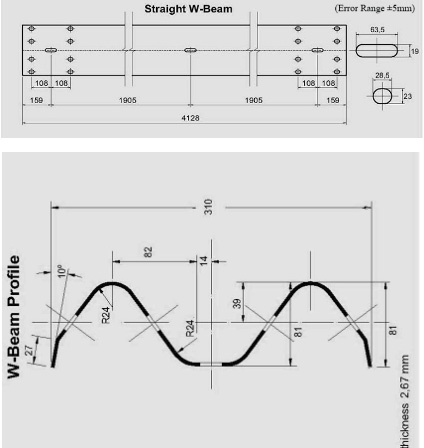
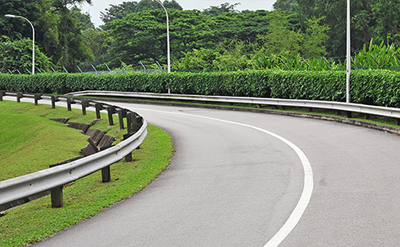
Applications of W-Beam
a. Highways, Flyovers and Bridges.
b. High Embankments/Sharp Curves.
c. High Density fast moving traffic areas in cities.
d. Median barriers as road separators.
e. Protection from trees, rocky areas etc.
f. Hilly terrain, Ghats, curves, high embankments.
g. Test tracks in automobile industry, factories, and mines.
h. Mass housing complex, townships.
i. Airports, Railway stations and parking places
Advantage of W-Beam :
- Reduced Traffic Jams and Congestion : The crash barriers have a significant influence on decreasing traffic congestion and bottlenecks. Less traffic congestion leads to safer and more efficient driving.
- Increased Road Safety : Enhanced highway and road safety resulting in fewer accidents. The crash barriers are useful in preventing an out-of-control car from entering the opposing lane, therefore avoiding direct collisions.
- Low Maintenance: The crash barriers require less maintenance than any other type of road safety barrier. They are tough and can readily sustain severe hits. The crash barrier is designed to last at least 30 years with minimal maintenance.